Monday, April 10, 2006
Replacing the Maid
HR6 Humanoid Robot: Your Personal Assistant and Entertainer
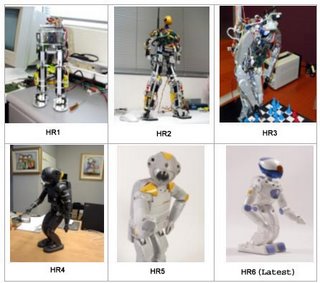
Car-bot, the Grand Challenge
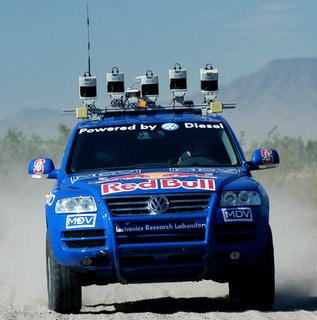
Cool Robot designed for deployment in Antarctica
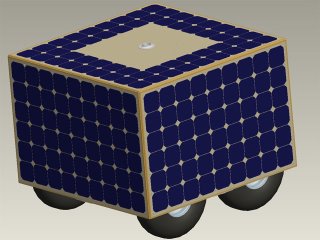
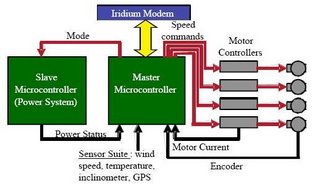
Sunday, April 09, 2006
HONDA ASIMO - the future
After motocycles, cars and power products, Honda has taken up a new challenge in mobility – the development of a two-legged humanoid robot that can walk. The aim of the function for the robot in the human living space was to create a partner for people, a social robot. From this challenge came the HONDA ASIMO, Advanced Step in Innovative Mobility. ASIMO is designed to operate in the real world with its abilities to walk smoothly, climb stairs and recognise people's voices.
The ASIMO is scheduled for use in a pedestrian safety program named “Step to Safety with ASIMO”. This is a program where ASIMO will help students learn the safe and responsible steps to road-crossing using its human-like capabilities. Using ASMIO in this program is beneficial as such a robot will catch the attention of the young children and allow them to pay more attention to the safety steps being taught.
Besides this, ASIMO has been involved in many entertainment events such as performing for visitors at Aquarium of the Pacific, dancing with the host on the Ellen DeGeneres show and even walking down the red carpet for the premiere of the movie, “Robots”. The interactive nature of this robot has endeared itself to viewers from all over the world.
Videos of ASIMO in action can be viewed on the website at this link "http://asimo.honda.com/inside_asimo_movies.asp". It is fascinating how the movement of the ASIMO is so human-like, from the dipping of the shoulders to the turning of the hips when running. Look out for the particular video "NEW MOBILITY". You will be amazed by the human-like manner in which the robot comes to a stop after running. You can't help but be reminded of a human runner after you watch that clip.
Honda engineers created ASIMO with 26 degrees of freedom to allow it to mimic human movement as much as possible. For the technical part, we shall concentrate on the movement component.This robot’s walk is modeled after a human being with the human skeleton used for reference when locating the leg joints. The joint movement was calibrated after research carried out on human walking on flat ground and stairs. From there, the centre of gravity of each leg was modeled after that of the human body. Similarly, to obtain the idea torque exerted on the joints during motion, vectors at the joints during human motion were measured.
Besides this, sensors were also implemented. These were based on the 3 senses of balance that humans have, namely speed by the otolith of the inner ear, angular speed by the semicircular canals and deep sensations from the muscles and skin, which sense the operating angle of the joints, angular speed, muscle power, pressure on the soles of the feet and skin sensations. From this, the robot was equipped with a joint angle sensor, a 6-axis force sensor and a speed sensor with gyroscope to determine position.
To achieve stable walking, three main posture controls are used, namely floor reaction control which maintains firm standing control of the soles of the feet even during floor unevenness, target ZMP (Zero Moment Point where inertial force is 0) control which is the control to maintain position by accelerating the upper torso in the direction in which it threatens to fall and finally, foot planting location control which is the control using side steps to adjust for irregularities in the upper torso caused by the abovementioned target ZMP control.
Finally, a new two-legged walking technique allowed for more flexible walking by creating prediction movement control. For example, when humans wish to turn a corner, they will shift their centre of gravity towards the inside of the turn. With the Intelligent Walking Technology, ASIMO is able to predict its next movement in real time and adjust its centre of gravity correspondingly in preparation for any turns.
Reference: http://asimo.honda.com/inside_asimo.asp?bhcp=1
Pictures can be found at http://asimo.honda.com/photo_viewer_news.asp
Surgical Robotic systems
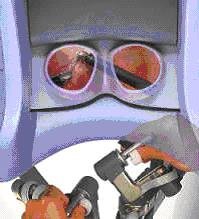
Robots utilized in medicine, especially in surgeries, serve as assistance to doctors in their role of dispensing medical treatment to patients and even enhance their services. An important aspect is the improvement of the surgeon’s dexterity during surgery. No matter how skilled a surgeon is, there is always a slight tremor of the hands. Morever, operations of highly sensitive and confined body spaces like the brain, heart and prostate, can be performed by only a limited number of surgeons who are skilled and experienced enough for the task. With the advent of such assistive robotic surgical systems as the Automated Endoscopic System for Optimal positioning (AESOP), the Da Vinci surgical system and the ZEUS robotic system, hand tremors are a thing of the past.
The robotic limbs, holding onto the surgical instruments, could execute movements that are as minute as a millionth of an inch. The march towards non-invasive surgery motivates the development of such systems. Increasing number of heart by-pass surgeries are now performed through pin-hole incisions, via a robot-assisted endoscopic extensions. The four-arm Da Vinci system offers great precision and eliminates the need for inverted manipulation of the surgical instruments as the on-board processor can translate the surgeon’s hand movements correctly into the desired manipulation of the surgical instruments. There is also three-dimensional imaging capability via a camera attached to one of the arms.
At the Medical Centre of Hershey, Dr Ralph J. Damiano Jr., used a surgical robotic system that has a camera that magnify views of operation procedures by a power of 16.
Voice commands-driven robots are also a possibility in another up-coming system, called “Hermes”. This will the advent of the “intelligent” operating theatre, in which the doctor just focus on making critical surgical decisions and “asks” the robot to execute the moves.

In use at 280 hospitals now is the AESOP system.
Using the Zeus or da Vinci system, largely invasive surgeries such as heart bypasses, can be made less painful and complicated. Traditional techniques of making a 1-foot-long incision on the chest and thereafter prying open the rib cage to reveal the heart is now replaced by cutting just a tiny hole of 1 cm through which endoscopic extensions containing fibre optics and surgical tools are inserted.
References:
How robotics will work, http://electronics.howstuffworks.com/robotic-surgery1.htm
Robotic Surgery, http://ipp.nasa.gov/innovation/Innovation52/robsurg.htm
Laproscopic Surgery, http://www.lapsurgery.com/robotics.htm#ROBOTS%20IN%20LAPAROSCOPIC%20INGUINAL%20HERNIA%20REPAIR
In Vivo Robots for Remote surgery
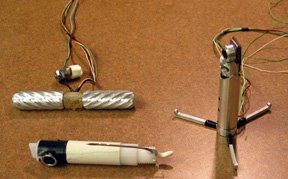
"All eyes on the line"
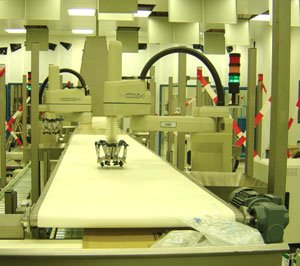
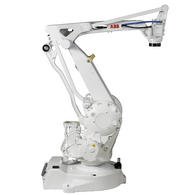
Conversational Humanoid
Microbots: Micro Life-savers.
Microbots: Micro Life-savers.
Introduction
Rapid advancement in nanotechnology has now allowed the production of smaller and smaller robots. Prototypes of robots, which measure only a few micrometers across, are already being made, and it is only a method of time before, it would be mass-produced. Kazushi Ishiyama, from the
Drug delivery:
The main drawback of conventional drug delivery methods is the difficulty in delivering the exact dosage of drugs to the precise target. The digestive system of the patient breaks down a large portion of the drug, before it could reach its intended target. One method of bypassing this problem is to take larger doses of medications. However, overdosing usually carries harmful side-effects and might even be lethal. Although injections do not have this problem, they are expensive and are difficult to self-administer. Microbots provide an elegant solution to this problem.
A microbot could be injected directly into the bloodstream of the patient, where it can be used to deliver required level of medications directly to malignant cells (where it is needed) at regular intervals. Thus there is no longer any problem of taking in too large or too small of a dose of medications, and there is no longer any need for a trained medical professional to be around, each time the patient requires a dose of medication.
Destroying cancerous cells
The conventional method of cancer treatment involves zapping cancerous cells with radiotherapy. While it is effective in eliminating the cancerous cells, the healthy cells around cancerous cells are often killed in the process, thereby weakening the immune system of the patient. However, microbot can be used to eliminate the cancerous cells, without harming the healthy cells around them. Kazushi Ishiyama’s microbot prototype is a rotating magnetized screw, which can be used to as a form of cancer treatment. The microbot is first injected into the patient, where it will burrow straight into the cancerous cells and unleash a hot metal spike to destroy them.
Technology behind the Microbot
The microbot is based of cylindrical magnets and is shaped like a small screw. The microbot is controlled by applying a three-dimensional electro-magnetic field, which will control the spin and direction of the microbot. Due to its small size, the microbot does not carry with it its own power unit, instead it is powered by the electro-magnetic field. By varying the pulses of the magnetic field, the temperature of the microbot could be increased, such that it is hot enough to burn away cancerous tissue. The microbot is strong enough to burrow through a 2cm thick steak in just 20 seconds.
Drawbacks
While the microbot is small in size, it might still be fatal if it accidentally blocks a blood vessel. Thus doctors are still apprehensive about testing the prototype on humans. Because lives are at stake, medical robotics usually requires an exceptionally stable control system. Thus there is a need to have a stable control system, such that the microbot will almost never stray into blood vessels. Another solution would be to further reduce the size of the microbot, until the extent that it will not block a blood vessel even if it accidentally strays into one.
Given enough time, I am sure that these problems would be overcome and we will see microbots being used to save countless lives.
Reference
http://news.bbc.co.uk/1/hi/health/1386440.stm
http://www.dietarysupplementnews.com/archives2001.htm
http://server.admin.state.mn.us/issues/scan.htm?Id=1355
http://www.pathfinder.com/asiaweek/magazine/2001/0803/pioneer3.html
Saturday, April 08, 2006
Robotic Probe of the Great Pyramid of Egypt


Pyramid Rover being deployed (left) and inside the square tunnel (right)
Robot explorers have indeed been playing very important role in other archeological expeditions, helping archeologists unearth ‘lost’ civilizations and solve the underlying ancient mysteries buried underground. So popular the participation of robots in these projects, scientists have come up with a branch of engineering specializing in this area, called “Ancient Engineering”. Who knows what robots may discover next time...
Da Vinci - Robotic Assisted, Minimally Invasive Cardiac Surgery
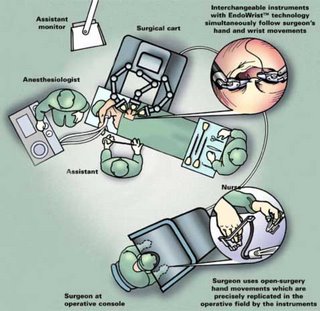
Enon -- Fujitsu's Service Robot
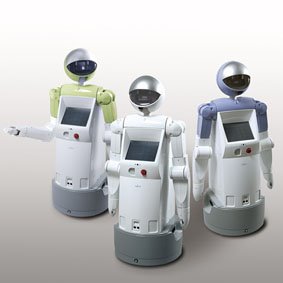

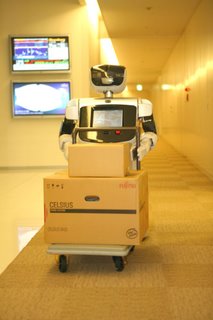
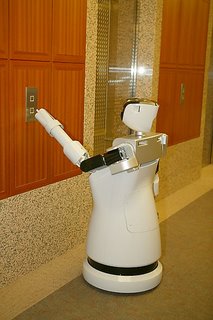
Underwater, Unmanned, Untethered - A new paradigm in undersea surveillance
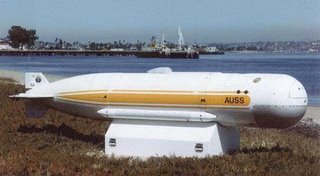
Introduction Before the advent of the Advanced Unmanned Search System (AUSS), researchers faced a tradeoff between using tethered and untethered undersea surveillance robots. The untethered robots obviously had more freedom and range of movement, without chances of wires getting caught or tangled, but they lacked the capability of transmitting real-time information to the user. Furthermore, an untethered vehicle can move at relatively high speeds and perform sharp, precise maneuvers, or it can hover stably without expending power fighting cable pull. The AUSS, developed by Richard Uhrich & James Walton at the Naval Command, Control and Ocean Surveillance Center of SPAWAR Systems Center in San Diego, is an underwater vehicle which is both unmanned and untethered. Communication with a surface ship is accomplished by means of underwater sound, by means of a sophisticated digital acoustic link. Its operation is similar to that of a space probe, with the robot proceeding on its own, and able to receive real-time instructions at any time. Advanced abilities of the AUSS include going to a newly commanded location, hovering at a specified altitude and location, executing a complete search pattern, or returning home on command.
Purpose
The purpose of AUSS is to improve the Navy's capability to locate, identify and inspect objects on the bottom of the ocean up to depths to 20,000 feet. The vehicle utilizes sophisticated search sensors, computers, and software, and it is self-navigating. When commanded to do so, it can autonomously execute a predefined search pattern at high speed, while continuously transmitting compressed side-looking sonar images to the surface. The operators evaluate the images and supervise the operation. If they wish to further check out a certain object, they can order the vehicle to temporarily suspend sonar search and swim over for a closer look using its scanning sonar or still-frame electronic camera. Each camera image is also compressed and transmitted to the surface. If the operators see that the contact is not the object sought, a single command causes the vehicle to resume the search from where it left off.
Once the object sought is recognized, a detailed optical inspection can be conducted immediately. The AUSS offers multiple options for this, including:
- Previously transmitted images can be retransmitted at higher resolution.
- New optical images can be requested from different altitudes and positions.
- A documentary film camera can be turned on or off.
- If the object of interest is very large or found to be highly fragmented, the vehicle can perform a small photomosaic search pattern, taking overlapping pictures guaranteeing total optical coverage of a defined area.
How Acoustic Communication Works
As opposed to physical cables like fibre-optic cables, the AUSS communicates via sound. The acoustic link transmits compressed search data to the surface at rates up to 4800 bits per second, and sends high level commands to the vehicle at 1200 bits per second. Given the robot vehicle’s intelligence, the operator does not have to supervise it at each step. Instead, higher level commands of what to do (rather than how to do it) are given. The AUSS autonomously performs each task until it is completed or until the operators interrupt with a new command.
Navigation
The vehicle's computers use a Doppler sonar and a gyrocompass to perform onboard navigation.
Control
Generally, all critical loops on the robot’s control system are closed. This means that the operator does not have to employ joystick-like control of every movement. The intelligence and navigation of the AUSS allows the user to instruct it to move to a specified location, say a few miles away, and have the confidence that it will successfully navigate itself to that location without further input.
On the other hand, the operator has the freedom to give new instructions or interrupt some decision loop that is executing on the robot. This frees the AUSS from being limited to pre-programmed routines and allows the operator to apply his intelligence and experience to control the robot vehicle. Since images are fed back to the operator constantly, once there is something interesting the operator can instruct the AUSS to make closer investigation, in the variety of ways outlined above.
Image sensors
There are two ways of relaying search information back to the human operator – sonar and optical images. Sonar images can be generated faster and have a very large range, but the resolution is poor. Optical images, on the other hand, are taken at the range of a few feet and offer greater detail. Generally, if a human wants to take a closer look at any object, an optical image is necessary to confirm the status of the object.
Other specifications
The AUSS vehicle is designed to operate as deep as 20,000 feet. It is 17 feet long, 31 inches in diameter, and weighs 2800 pounds. The center section is a cylindrical graphite epoxy pressure hull with titanium hemispherical ends. The hull provides the central structure and all its buoyancy---no syntactic foam is used. The free-flooded forward and aft end fairings and structure are of Spectra, a nearly buoyant composite.
At its maximum speed of five knots, the endurance of the AUSS silver-zinc batteries is ten hours. Recharging requires 20 hours. Typical missions have been ten to fifteen hours. Three sets of batteries would allow AUSS to operate indefinitely, with only 3-1/2 hours between 20,000 foot dives.
Test results
In the summer of 1992 the system performed a series of sea tests off San Diego culminating in a 12,000 foot operation. AUSS conducted side looking sonar search at five knots, and performed detailed optical inspections of several objects which it found. It proved capable of sustained search rates approaching a square nautical mile per hour, including the time spent investigating false targets. The image shows a World War II Dauntless Dive Bomber identified by the AUSS.
Issues At this point, I will raise some issues for consideration. Here, unmanned vehicle means that low-level instructions on navigating and doing pre-programmed search are unnecessary. However, the AUSS still requires human supervision to detect unique objects, and to decide which objects to further investigate. This may result in problems in missions where there has to be acoustic silence, or where manpower is insufficient. Can a better algorithm and control system be developed such that the AUSS be equipped with sufficient intelligence to discern between interesting and trivial objects? Also, given the kind of technology that the navy employs in such robots for undersea surveillance, could such vehicles also be used for scientific research and oceanography at the same time? The deep oceans are still relatively unexplored and the information returned by such robots could prove invaluable to the scientific community and mankind in turn. Reference links:
Patients - Simulated

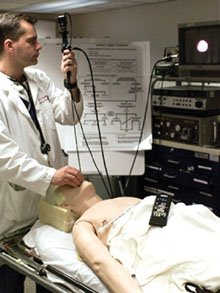
Friday, April 07, 2006
In future a traffic jam can be more than just time-consuming ...
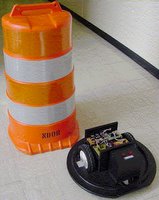
Robolobster - Military tools for land and sea operations
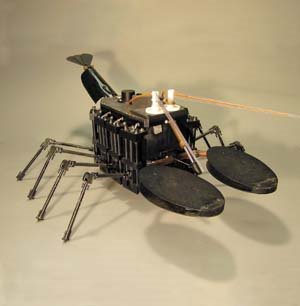
Fig 3: Robolobster movement on land